Blended tobacco is usually treated with flavoring agents such as cocoa and licorice powder to enhance tobacco’s taste and aroma. Some tobacco varieties also require humectants to help restore and maintain the moisture and pliability of the leaf, as well as restore natural sugars (without which can make the smoke irritating) lost during some post-harvest curing processes.
Thayer Scale Equipment for Casing, Flavoring and Drying Tobacco
In casing, and drying operations, tobacco moisture and weight are the most critical metrics to control and maintain. For decades, Thayer Scale Low Density Model “M” and “MXL” Weigh Belts have been helping producers control these variables.
To ensure that casing and flavoring agents are applied in-phase to blended tobacco, tobacco producers deploy Thayer Scale’s Scale Location Compensation (SLC) feature. SLC effectively moves the point of base tobacco measurement and flow rate control from the scale’s physical location within a conveyor to the point downstream where casing and flavoring agents are applied, better serving the response needs of the downstream process.
Unlike basic time delays, SLC provides positional (distance) transformation of weight data to eliminate process lag and properly sequence additive delivery when changes in total flow across a given weigh belt occur. SLC maintains sequencing even when variable speed equipment is interposed between a weigh belt and the casing cylinder.
To maintain the distinct flavor profiles associated with various cigarette brands on a consistent basis, tobacco producers rely on specialized Thayer Scale Loss-In-Weight systems to deliver powdered base flavoring agents into casing systems on an accurate and repeatable basis. Each Loss-In-Weight system features a mass counter-balanced weight sensing system interposed between a tilting intermediate bulk handling container discharge station / metering auger assembly and a single load cell.
Using powered pallet trucks, operators load a side door intermediate bulk-handling container filled with the required flavoring onto the Loss-In-Weight system. An onboard pneumatic system tilts the container frame until the container mates with the seal on the metering auger. The operator then inserts a key wrench through an access port and rotates the locking cam on the container door, allowing the contents of the container to flow into the metering auger.
Once a container is loaded and properly positioned, the Loss-In-Weight instrumentation system seamlessly interfaces with the processing system’s supervisory control system and accurately dispenses the correct amount of flavoring agents as called for by a given recipe SKU without operator intervention. The system also signals when a container is empty and needs replacement.
Mass counter-balancing optimizes measurement accuracy by maximizing the load cell utilization factor – the percentage of a load cell’s rated output that is available for actually weighing material.
The load cell’s capacity is based on the net weight of the container’s contents, rather than the gross weight of the material combined with the apparatus (container, discharge station and metering auger). The weight sensing system combines high sensitivity to meet a given recipe’s needs, with extreme ruggedness – tolerating shock and impact associated with installing and removing totes without damage or calibration drift.
During dosing operations, Loss-In-Weight Feeders are particularly vulnerable to external disturbances that occur periodically or randomly during normal operation. Other manufacturer’s Loss-In-Weight feeders assume disturbances either exist or do not exist, and that when a disturbance is detected, measurements cannot be made. Upon detection, these 2-state systems interrupt closed loop gravimetric control and lock the controller output at its last value, adversely affecting measurement accuracy.
Conversely, Thayer Scale Loss-In-Weight feeders feature a disturbance control system that assumes disturbances are always present but that they vary in intensity and according to type, and that when a disturbance is detected measurements can still be made. Upon detection, Thayer Scale’s disturbance protection limits the magnitude of the error signal presented to the control algorithm under normal weight loss control, allowing the unit to regain control much faster after a process upset by minimizing control loop oscillations without interrupting closed loop gravimetric operation.
The disturbance protection parameters are field programmable to protect the system against the most encountered lower intensity disturbances without relinquishing weight-based control. Additional programmable functionality protects against larger and longer lasting sporadic disturbances.
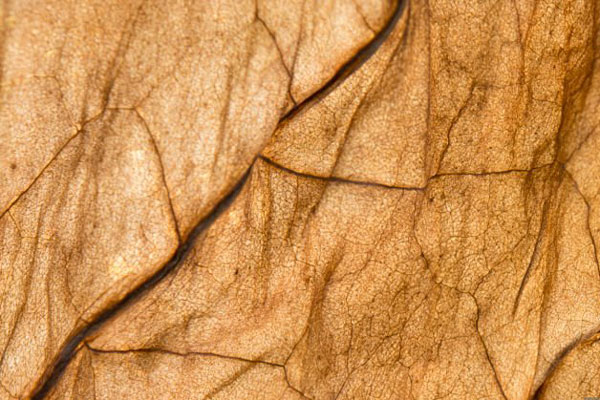
Each manufacturer has unique recipes that define their brands.
Casing is the process that applies these recipes to the tobacco blend, providing initial flavoring and soothing the smoking experience. Spraying these ingredients on the product as it passes through a cylinder is the most common casing method used today. Spray cased tobaccos tend to be fluffier than tobaccos cased with other methods.
After casing, the blend is finely cut and final flavors such as vanilla, rum, whiskey or cherry are applied to provide the blend’s “top notes”.
Finally, the blend passes through a drying cylinder to reduce moisture. Only after the moisture is at an optimal level, is the blend (filler) is ready for cigarette manufacturing and final pack.

Weighing equipment for the processing of tobacco
Weighing equipment for the tobacco industry includes:
Weigh belts
- Designed for light-density material handling in light loading applications (Model M-LD and MXL-LD)
- Available with open or enclosed construction
- Built to accommodate to new or existing process streams
Loss-in-weight feeders
- Auger discharge
- Vibratory pan discharge
- Feed rates from grams/minute to tons/hour
Flexible conveyor belt scale designs that support changing configurations
Hopper and silo flow aids
- Provides consistent, uninterrupted flow of material